Hosokawa Micron Powders GmbH has been a member of the Learning Energy Efficiency Network (LEEN) of RheinEnergie AG since January 2020. The project aims at further reducing the energy consumption and CO2 emissions of the participating companies on a permanent basis – by at least 5% every year. On the 6th February 2020, the first workshop of the Industry-LEEN was held in the Niehl 3 gas and steam turbine power plant of RheinEnergie AG.
Network for the transfer of energy efficiency know-how
LEEN is a learning energy efficiency network. What this means is that several companies from different branches get together in order to exchange experience on the subject of energy efficiency. The company delegates exchange information and know-how with each other, learn about new solutions and concepts, and discuss technologies, processes, procedures and strategies.
The objective is to maximise the joint level of knowledge and to thus improve the energy efficiency of all companies in the alliance. The target regarding CO2 emissions and energy consumption is around 5% reduction per year. Besides the pure transfer of know-how, a high level of investment is naturally necessary which, however, amortises in the long run as a result of the energy conservation.
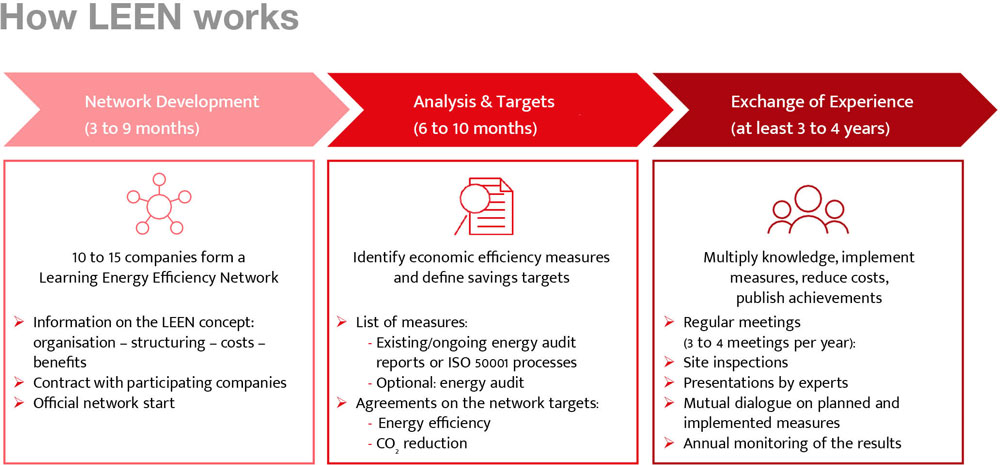
This is how a Learning Energy Efficiency Network functions (figure: RheinEnergie).
In total, there are three LEEN networks from the sectors of industry, buildings and hospitals. Hosokawa is one of 16 companies within the Industry Network. The project is coordinated by the companies LEEN GmbH, RheinEnergie AG as well as the TH Köln (Cologne technical college), who also provides scientific support. Network meetings which take place several times a year constitute an essential component of the cooperation.
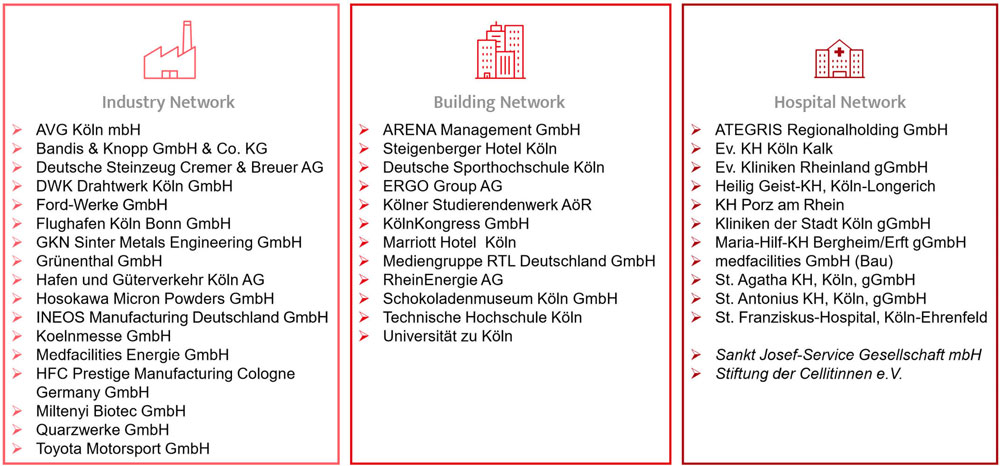
These are the participants of the Cologne Energy Efficiency Networks (figure: RheinEnergie).
Energy efficiency at Hosokawa
At its business location in Cologne, Hosokawa Micron Powders produces over 14,000 tonnes per year of a vast variety of materials using meanwhile more than 18 production-scale systems in three-shift operation for almost 100 customers. The focus is on the ultrafine grinding of chemical and mineral materials down to fineness values of less than 10 µm. This comminution process is extremely energy-intensive. Around 13.5% of the total costs are energy costs. Because of this and for reasons of economy and ecology, the aim is to identify further possibilities of saving energy in order to constantly optimise what is already an extremely high energy efficiency.
Hosokawa’s managing director Dr Christoph Wadenpohl explains: “In the light of the global climate change, energy savings resulting from continual process optimisation are far more than an essential part of business management. They constitute the absolute order of the day with respect to a world worth living in for the coming generations. The exchange of views and ideas with experts from other companies holds the promise of new insights and perspectives which we are pleased to adopt. Because ultimately, the most energy-efficient kilowatt hour is the one that is not consumed.”
Already today, Hosokawa is certified according to ISO 50001. Substantial investments aimed to increase the efficiency at Hosokawa have already been made or are in the pipeline. These measures include:
- the combination of three highly efficient rotary screw and turbo compressors with an installed electric load of altogether 1.5 MW to generate 31 million m³ of compressed air per year;
- integrated heat recovery with the rotary screw compressors for heating the shop floors and the administration building;
- installation of a “Comprehensive Learning Energy Management” module (GLEM 4.0) for continuous monitoring and for connection to a remote monitoring system;
- use of oil-free system technology to meet the highest quality standards;
- performance of annual compressed-air audits to ensure continuing optimisation and identification of efficiency measures;
- step-by-step expansion and renewal of the compressed air station up to an installed electric load of altogether 2.3 MW;
- change-over of the illumination in the buildings to LEDs and introduction of multiple-glazing.
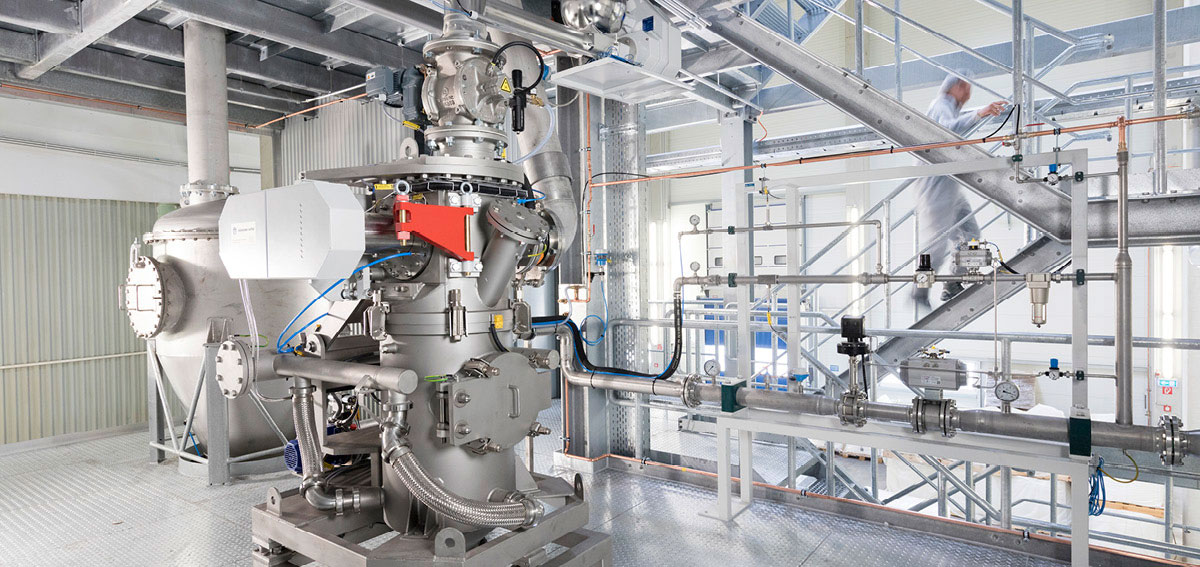
Air jet mill at Hosokawa (photo: Hosokawa)
First LEEN working session in the highly efficient Cologne cogeneration plant Niehl 3
On the 6th February 2020 and under the patronage of the state minister for economic affairs in North Rhine-Westphalia, Prof. Dr Andreas Pinkwart, the first workshop of the Industry-LEEN took place in the Niehl 3 gas and steam turbine power plant of RheinEnergie AG.
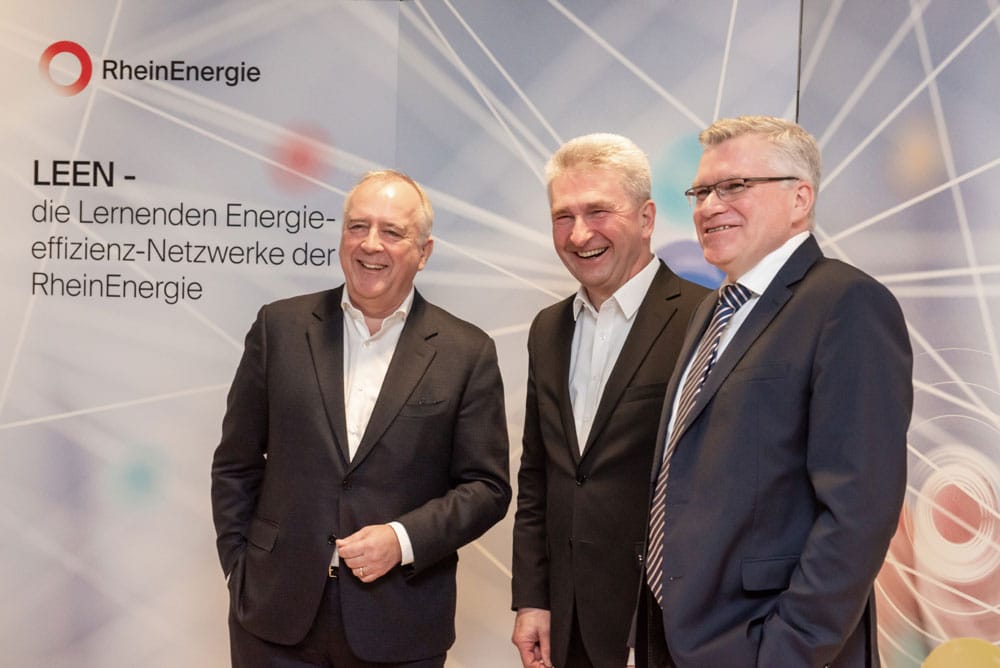
Gunnar Herrmann, chairman of the board of Ford-Werke GmbH, Prof. Dr Andreas Pinkwart, state minister for economic affairs, innovation, digitisation and energy, and Achim Südmeier, head of sales at RheinEnergie AG, in early January at the presentation of the three Cologne energy efficiency networks (from left to right; photo: RheinEnergie).
Besides introduction of the participants and the LEEN concept, a guided tour of the power plant was also on the agenda. The location was perfectly chosen for the topic of energy efficiency and at the same time a highly motivating example: the Niehl 3 power plant has an efficiency of 88% and is thus one of the most efficient and modern power stations in the world.
Already at the premiere, the network partners entered into an active dialogue concerning their strategies, measures and working methods as well as technologies and processes on the sector of energy efficiency in order to identify promising approaches to increasing the energy efficiency.
Emil Issagholian from RheinEnergie summarises the results of the kick-off meeting: “Today has revealed that many technical managers and energy managers see themselves faced with similar challenges. And because all partners carry out regular energy audits as defined in DIN EN 16247 or have already put an energy management system in accordance with ISO 50001 into place, the identification and performance of energy efficiency measures are always the focal point of daily operations. Moreover, the constantly changing regulatory requirements designed to fulfil the standards and the increasing pressure to reduce the CO2 emissions confront the participants with additional challenges. In LEEN, it is precisely at these ‘points of pain’ that we want to make a start.”
The 2nd network meeting of the Industry-LEEN is scheduled for the 3rd September 2020. Planned are guided tours of the participating companies as well as presentations. Over and above this, a continuous exchange on the planned and implemented measures as well as results monitoring are on the agenda.